PE Cold Applied Tape Making Machine for Pipeline Anticorrosion Wrap
Product Description
Cold-applied anticorrosion tape making machine is designed for producing the PE tape for protection of underground or overhead pipelines in oil, gas, petrochemical, and wastewater industries.
The equipment mainly consists of three parts: PE base film extrusion production line, Adhesive coating equipment, and slitting equipment.
Technological processes
The production process of cold-applied tape typically includes the following main steps:
-
Base Film Extrusion
-
Raw Material Preparation: Polyethylene (PE) is prepared as the base film raw material.
-
Extrusion Molding: The raw material is heated and melted in an extruder, then molded through a die to form a continuous base film.
-
Cooling and Shaping: The extruded base film is cooled and shaped using cooling rollers to ensure uniform thickness and consistency.
-
Adhesive Coating
-
Adhesive Preparation: Butyl rubber are prepared to ensure proper viscosity and stability.
-
Coating Process: The adhesive is evenly applied to one or both sides of the base film using coating equipment to form an adhesive layer.
-
Slitting
-
Slitting Preparation: The coated base film roll is prepared, and the parameters of the slitting equipment are adjusted.
-
Slitting Operation: The wide roll is slit into cold-applied tapes of the required width using slitting equipment.
-
Winding and Packaging: The slit cold-applied tapes are wound into rolls, packaged, and prepared for shipment.
Product Parameters
Equipment List
PE basing file extrusion line
|
Equipment Name |
Quantity |
1 |
Vacuum automatic feeder |
1 |
2 |
Hopper dryer |
1 |
3 |
SJ-75X30 extruder |
1 |
4 |
Hydraulic screen changer |
1 |
5 |
Die head mold type 1000 |
1 |
6 |
Multi-roller tape-casting machine |
1 |
7 |
Winding machine |
1 |
8 |
PLC computer control system |
1 |
Adhesive coating machine
No. |
Equipment Name |
Qua. |
1 |
Frame |
1 unit |
2 |
200N·M Magnetic powder brake + Silicone stick 1300mm with corona processor |
1 unit |
3 |
100N·M Magnetic powder brake |
1 unit |
4 |
100N·M magnetic powder clutch |
2 unit |
5 |
200N·M magnetic powder clutch |
1 unit |
6 |
Screw |
1 unit |
7 |
Force-feed device |
1 unit |
8 |
Constant pressure system |
1 unit |
9 |
Adhesive delivery pipe |
1 unit |
10 |
Winding machine |
1 unit |
11 |
Unwinding machine |
2 unit |
12 |
Coating compound equipment |
1 unit |
13 |
Main engine frequency converter |
1 unit |
14 |
Extruder frequency converter |
1 unit |
15 |
Thermal switch |
1 unit |
16 |
PLC |
1 unit |
Our Advantages
-Adopt advanced technology
-Stable operation
-High degree of automation, saving labor costs
-Good quality, meets international standard
-Supply full completed production solution: design, installation, commissioning,training
-Share you 389 sets of production experience from all the world
-Having 9 professional senior engineers
-Having a high-end plastic machinery equipment expert workstation in China
Customer cases
Company Profile
Qingdao Huashida, a global plastic extrusion equipment R&D manufacturer and solution provider, 70% of our customers from Europe, the United States, the Middle East and Southeast Asia and other overseas countries. Huashida's R&D and manufacturing insulation pipe production line is widely used in municipal heat, sewage, water supply, natural gas and communication pipe network construction, crude oil pipeline transportation and agricultural irrigation. Relying on our innovation and product strength, we have provided customized technical services for more than 1000 manufacturers , including more than 400 domestic enterprises and more than 500 foreign enterprises and established a 24-hour global service response mechanism to effectively solve customer concerns.
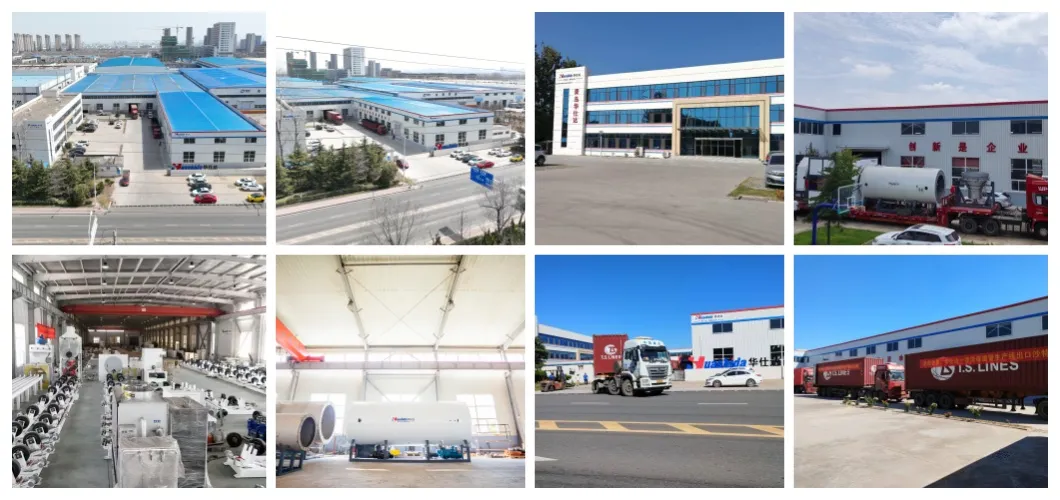
Our team
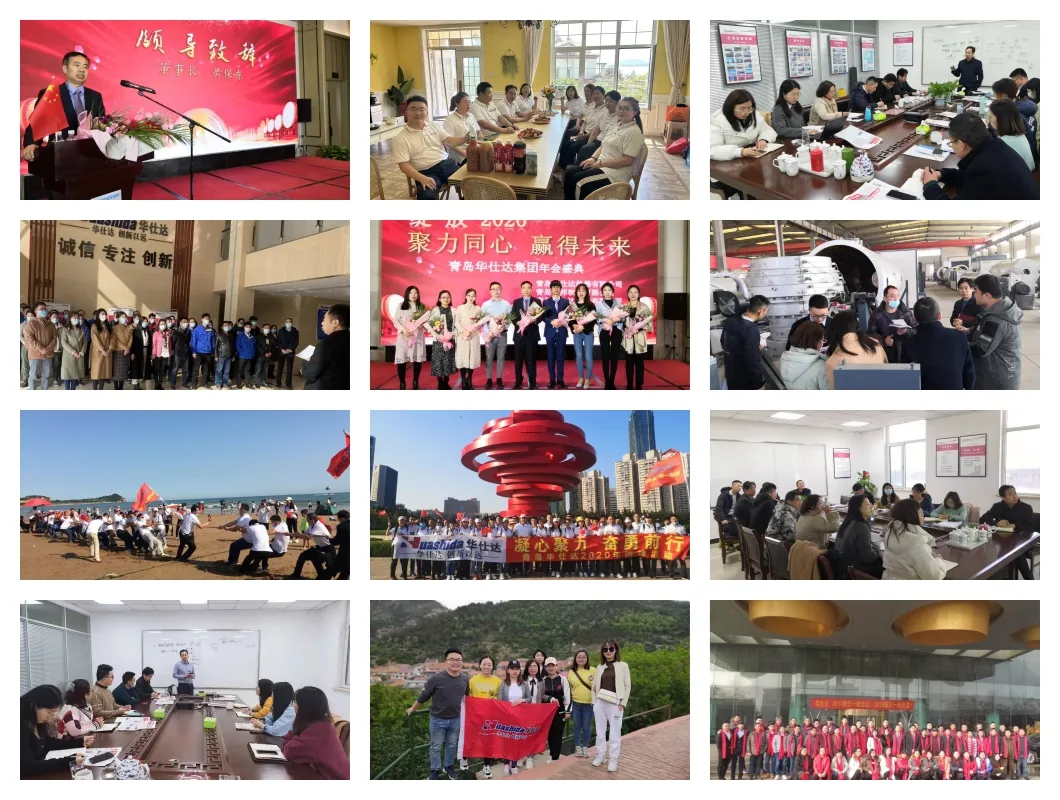
Delivery
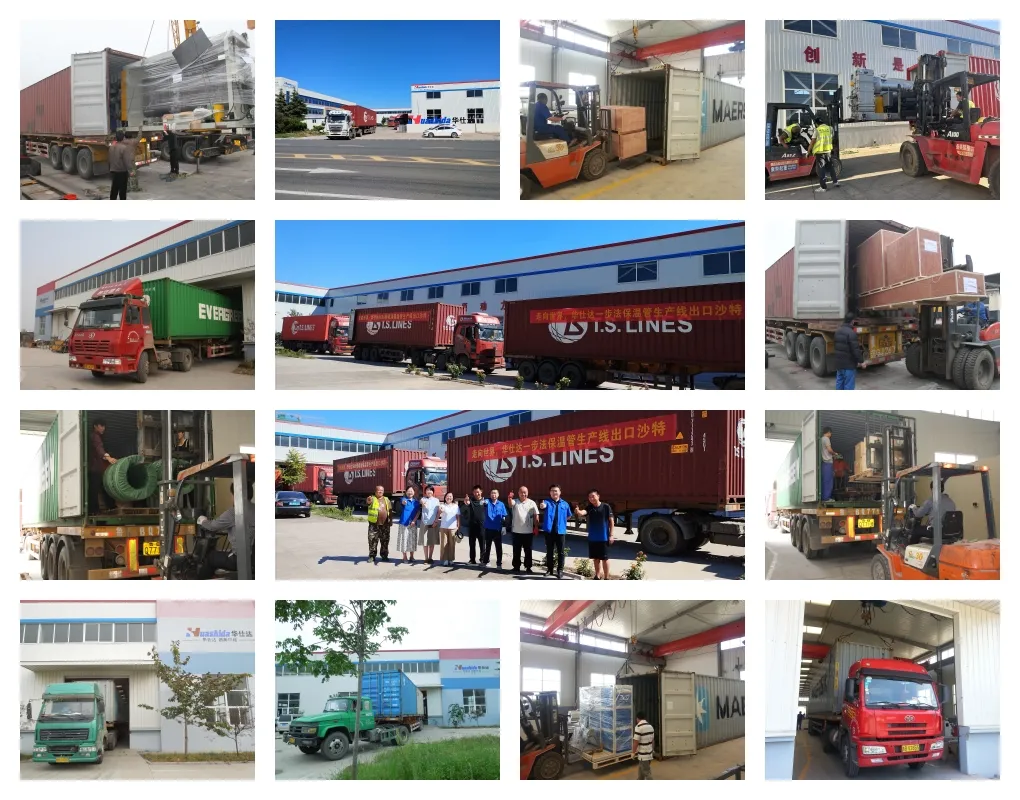
Exhibition
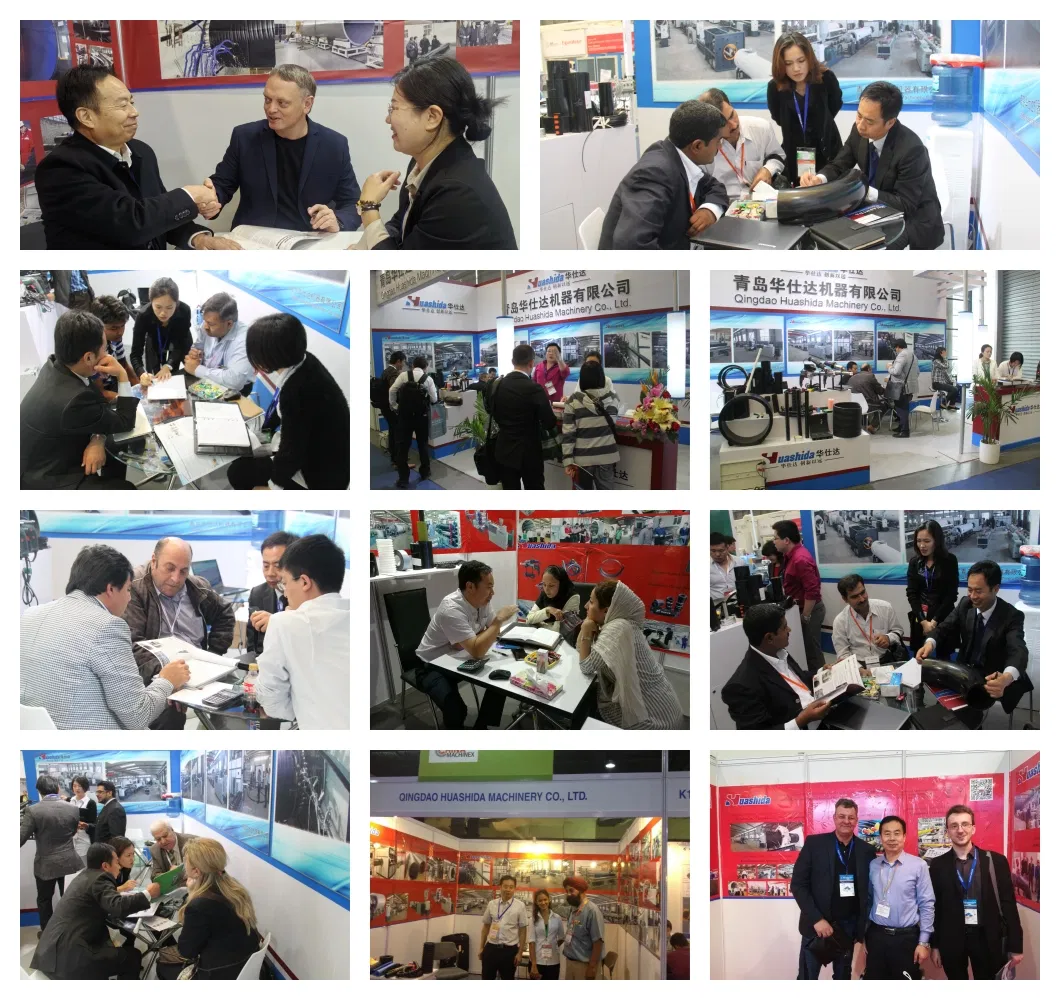
Certifications
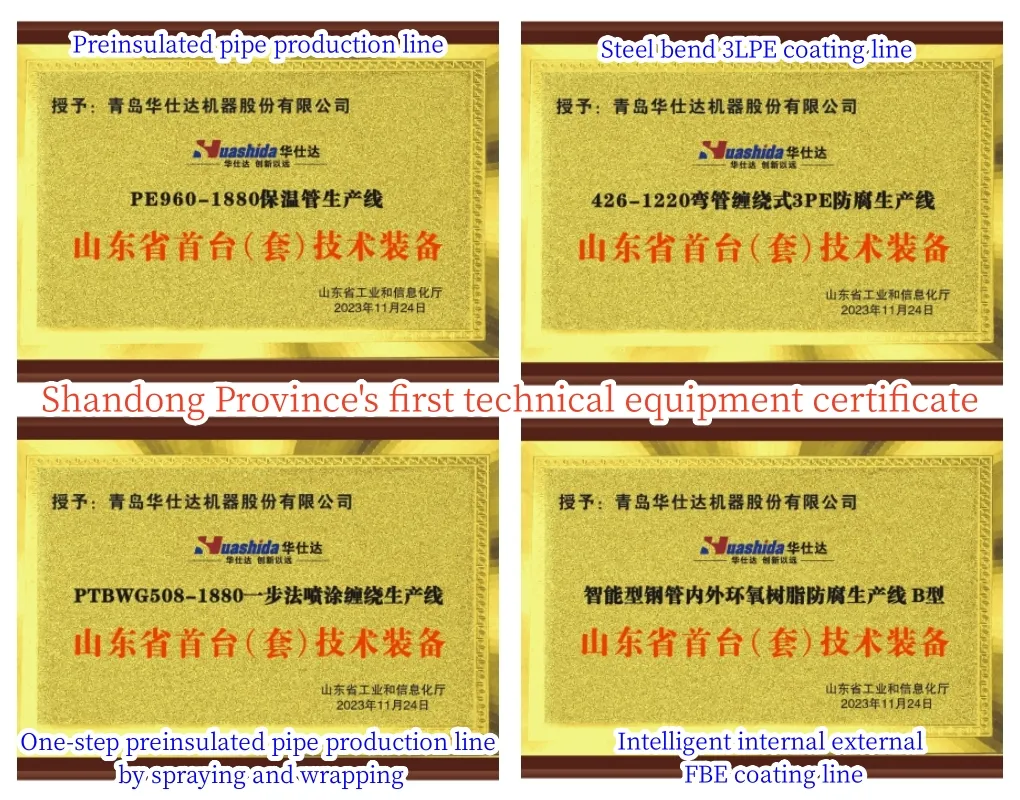
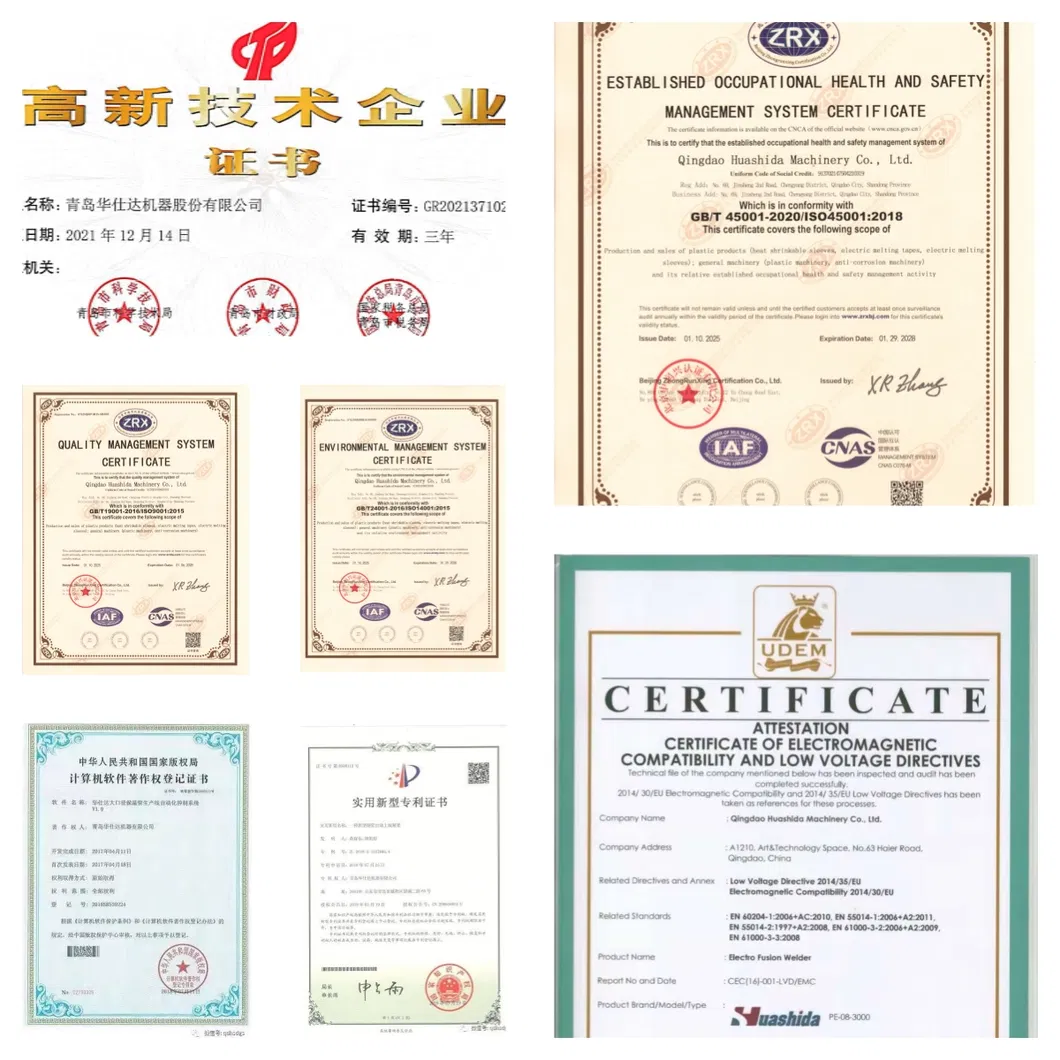